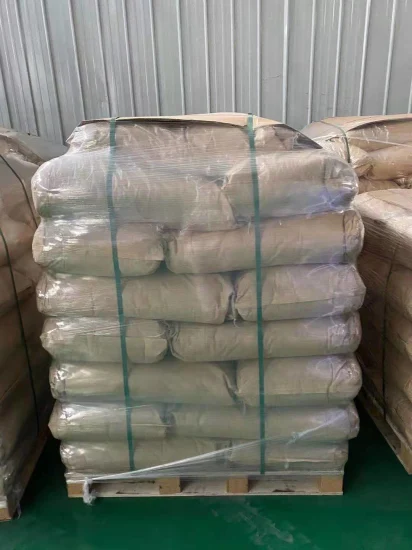
Metallic Coagent Zda, Zinc Acrylate (CAS: 14643-87-9)
Crosslinking with peroxide results in the formation of a covalent bond as shown in (A). This carbon-carbon bond is quite
Description
Basic Info
Model NO. | Saret SR633 |
Name | Zinc Acrylate |
CAS Registry Number | 14643-87-9 |
Transport Package | 20kg/Bag or 20kg/Drum |
Specification | 99% |
Trademark | CapatueTM |
Origin | P. R. China |
HS Code | 2931900090 |
Production Capacity | 100 Tons/Year |
Product Description
Abstract | ||
CapatueTM MCA-633 (Zinc acrylate (ZDA) with CAS number 14643-87-9) is a difunctional solid acrylate salt for use in peroxide cured elastomers(NBR, EPDM, CPE, BR, SRB, Silicone) where enhanced adhesion and dynamic properties are needed. It is an economical way to enhance the performance of peroxide-cured elastomers. CapatueTM MCA-633 (Zinc acrylate (ZDA) with CAS number 14643-87-9) is available at a fraction of the cost of other commonly used agents and yield comparable, even superior, mechanical properties. Its function is similar to Dymalink® 633 from Cray Valley of Total Company. | ||
Identification | ||
Chemical Name | : | Zinc acrylate |
Molecular Structure: | ||
Molecular Formula: | 2(C3H3O2).Zn | |
Molecular Weight: | 207.50 | |
CAS Registry Number: | 14643-87-9 | |
EINECS: | 238-692-3 |
Equivalents | ||
Dymalink® 633 from Cray Valley of Total Company Saret® SR633 from Sartomer Company | ||
Specifications | ||
Appearance: | Off-white powder | |
Specific Gravity: | 1.59 | |
Mesh: | ≥100 |
Mechanism |
In contrast, polysulfide crosslinks formed in sulfur cure are thermally weak but are mobile under stress and can slip along the hydrocarbon chain. This mobility has been used to explain the superior tensile and tear strength in sulfur cured stocks.
A. | B. |
Thus, this unique system embodies the best characteristics of both the peroxide and sulfur crosslink systems, giving high tensile and tear strength and excellent heat aged properties.
Feature and Benefit |
Peroxide curing with Capatue™ metallic coagents significantly enhances the performance of a variety of elastomers. These easy-to-handle, 100% reactive solids yield strong rubber-to-metal bonds and other highly desirable performance advantages, including:
Greatly improved heat aging
High tensile strength
High tear strength
Higher modulus
Higher hardness
Increased abrasion resistance
Improved resilience
Very high rubber-to-metal adhesion
2. Processing Advantages
Capatue™ Metallic coagents contain a patented none-nitroso scorch retarder for safe, easy processing.
High scorch safety
100% reactive solids
Non-volatile
Easily dispersed free flowing powders
Low odor
Available in pre-weighted, low melt polybutadiene bags
3. Cost Advantages
Capatue™ Metallic coagents are an economical way to enhance the performance of peroxide-cured elastomers. They are available at a fraction of the cost of other commonly used agents, such as HVA-2, and yield comparable, even superior, mechanical properties.
Application |
Rubber
Adhesive
Plastic
Cable & Wire
Processing |
1. Introduce the rubber stock and process for approximately 30 seconds. There is no need to "break down" the rubber before adding the formulation ingredients. The initial high rubber viscosity will aid in dispersing the additives.
2. Add the Capatue™ coagent and process just long enough to encapsulate the powder. This procedure minimizes sticking and interaction between the coagent and certain processing aids.
3. Add fillers and processing aids.
4. Add the peroxide curative.
5. Mix and blend as appropriate. Use standard processing temperatures and cycle times.
Dosage |
Packing |
Storage and Shelf Life |
The shelf-life of CapatueTM MCA-633 (Zinc acrylate (ZDA)) is six months from date of purchase when stored in its original packaging, temperatures between 10ºC and 32ºC and out of direct sunlight.
Our Contact
Send now